Bus door systems: electric or pneumatic mechanism? Take Ventura’s words for it
Electric propulsion has become an integral part of public transport and is slowly becoming the new standard for buses and coaches around the world. But what is the leading technology when it comes to mechanisms for door systems? Is it pneumatic or electric?
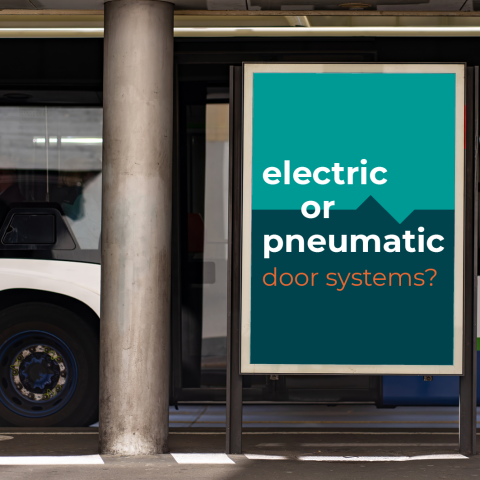
Authored and sponsored by Ventura Systems
Electric propulsion has become an integral part of public transport and is slowly becoming the new standard for buses and coaches around the world. But what is the leading technology when it comes to mechanisms for door systems? Is it pneumatic or electric?
Pneumatic driven mechanisms have served the bus market for many years, with electric mechanisms becoming more commonly used in recent times. This technology was introduced by the rail industry on automatic door systems and has almost completely eliminated pneumatic systems from their markets. One of the main reasons for the technological change towards automatic door systems is the request for better energy efficiency and lower costs within zero emission vehicles.
Understanding the differences between mechanisms is key to choosing the right technology.
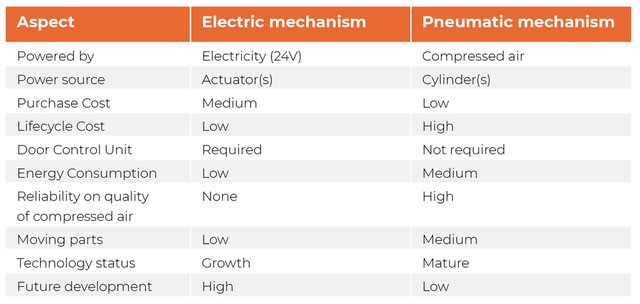
One door system, three key parts
Every door system consists of three key parts: the mechanism, the door leaves and the mounting kit (brackets/shafts). The mechanism, or drive system, delivers the power and the motion to open and close the door leaves. The power is transferred from the mechanism to the door arms and door shafts, that provide the motion to open the doors. The mechanism can be based on a pneumatic drive system using mainly compressed air, or an electric drive system using electricity.
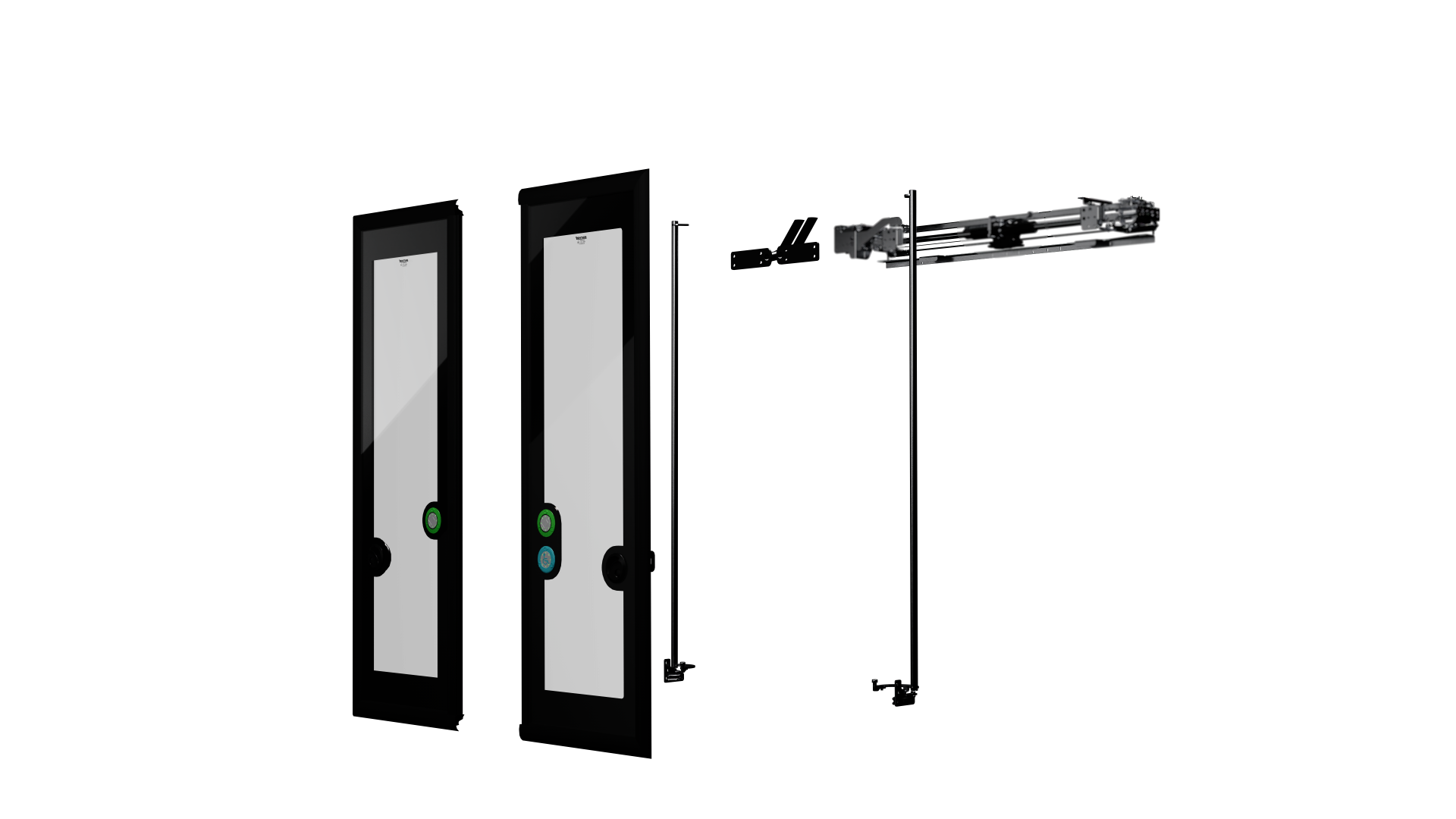
Bus doors’ opening: pneumatically or electrically?
Basically, both mechanisms operate the same and opening and closing speed are similar. The pneumatic mechanism supplies energy throughout cylinder(s) of compressed air, which are filled by the compressed air system in the vehicle. The electric mechanism supplies energy throughout actuator(s). An actuator converts the rotational force of an electric rotary motor into a linear movement to generate the requested linear force through the mechanism.
An actuator requires a dedicated control device, so a door control unit is mandatory, whereas for a pneumatic drive system the door control unit is optional besides additional valves for actuation. A door control unit manages the opening and closing of the doors, as well as safety features, emergency operation and communication with the vehicle’s control system.
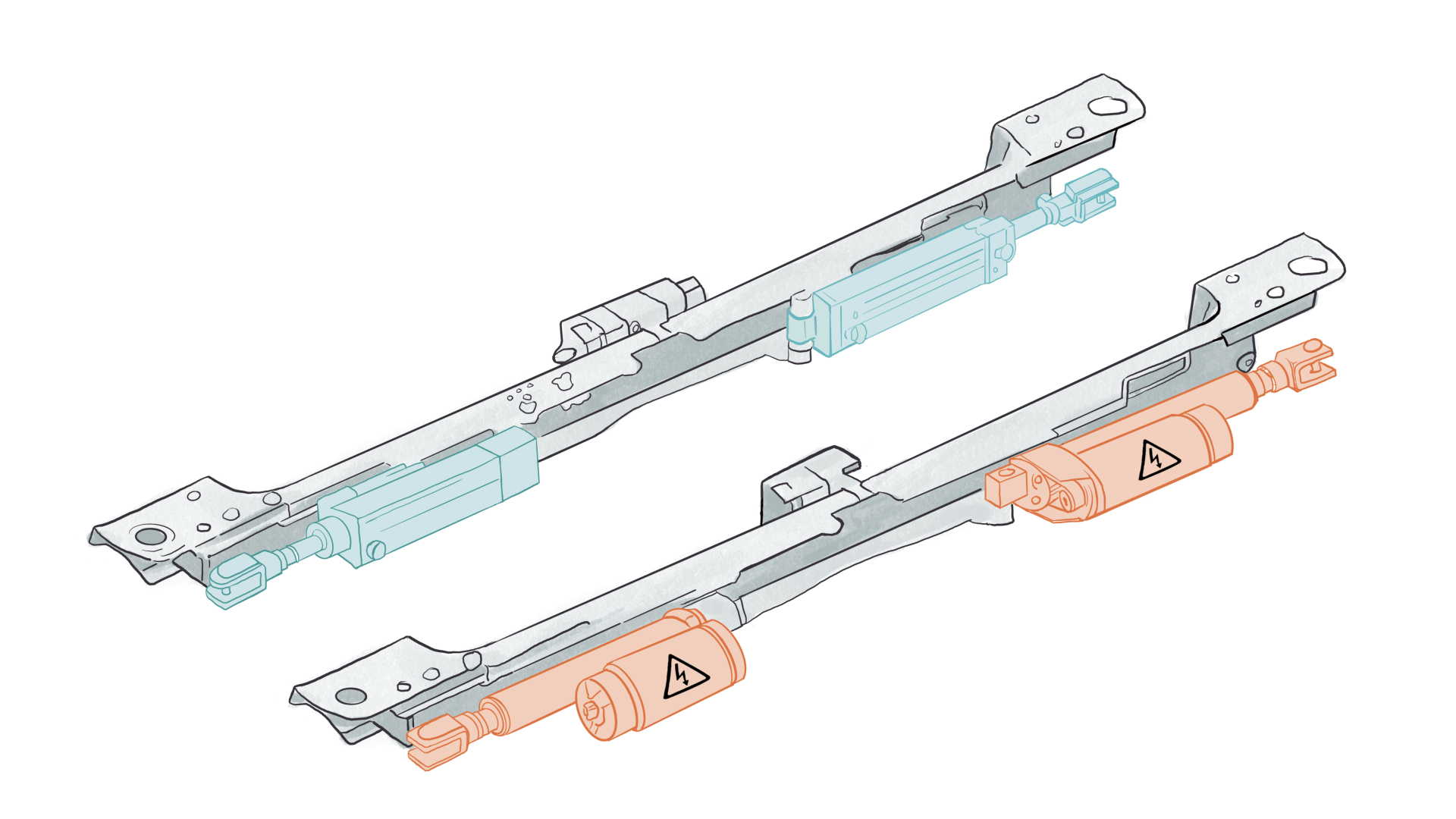
On energy efficiency of electric doors
An electric mechanism only requires (limited amounts of) compressed air for the emergency system that pushes the door leaves open when they are closed, unless a non-pneumatic emergency activation is installed. The emergency system needs to be pressurized to function but doesn’t consume compressed air. That’s why an electric drive system requires a smaller compressor and is more energy efficient, there is hardly any air pressure loss. This makes the system less dependent on a well-functioning air pressure infrastructure in the vehicle.
Another benefit of the electric mechanism is that it is more silent, due to the lack of use of compressed air for door operations. You won’t hear a ‘puffing’ sound when the door leaves are opening or closing, improving the passengers and driver experience due to the lack of unnecessary sounds.
If you are planning for the future, you would want to choose a drive system that is also supported in the future. That is the reason why most electric or hydrogen buses are being equipped with electric mechanisms. This technology will be the basis for the door systems on the vehicle for the next 15-20 years. Future technology that is developed based on an electric mechanism may not work on pneumatic mechanisms.
The issue of condensation
Water condensation is a natural occurrence and a byproduct of compressing air that could cause corrosion, quality issues or damage. With low temperatures the condensation could even freeze, causing even more damage. Electric mechanisms are less affected by low temperatures because of the limited volumes of compressed air. This also makes the mechanism less susceptible to air pollution.
Safety benefits of electric bus door’s mechanism
Due to new regulations and increasing demands for functional safety in door systems, electric mechanisms are becoming more popular. A pneumatic mechanism is generally ‘open loop’ controlled, meaning that the motion of the door is constant from the closed to the open position. With an electric mechanism, the movement of the door is ‘close loop’ controlled by the mandatory door control unit through speed and position monitoring. This means that the movement can be adjusted in unpredictable situations.
If the door control unit detects resistance during movement, it activates a parameterisable obstacle sequence, without the need for additional safety devices. In addition, the door control unit offers various safety features like overcurrent protection to protect the system against damages on external system currents.
The door control unit also works with sensors for additional safety features like a sensitive edge. It provides monitoring redundancies for diagnostics on each functionality. The door control unit offers the possibility to configurate the door operations to the preferences of the customer and makes monitoring and diagnosing very easy.
In summary, electrically operated door systems can provide a higher level of safety with less effort and cost than would be required for the pneumatic variant.
Maintenance and field support
Both the pneumatic as electrical mechanisms are reliable. The need of maintenance on pneumatic mechanisms is higher because the electrical mechanism has lower movement and locking forces during operation. The electric mechanism requires less adjustments and less maintenance which gives it a higher durability. The pneumatic mechanism must be adjusted over time due to the different behavior of compressed air on temperatures. This requires maintenance to be planned ahead.
Another benefit is that the combination between a door control unit and an electric mechanism gives more opportunities for diagnostics that can be used for condition-based maintenance.
The technology of electric mechanism control is the leading technology for door operation and will be improved, maintained, and developed over the next years. They are suitable for analytic purposes on functional safety measures.
On the other hand, the technology of electric mechanisms requires extra training and instructions for maintenance employees, as they are most known with the pneumatic technology. The electric technology needs to be transferred to the minds of the mechanics and drivers but also to processes and maintenance schedules. The introduction of unknown technologies will require more time and assets, in relation to using the more ‘standard’ pneumatic technology.
Technology development
Another important factor to consider is the technological development of mechanisms in the future, also in relation to development of zero emission vehicles. Because of the benefits, there is a lot of development on electric mechanisms whereas technology for pneumatic mechanisms is in a mature state and is less likely to be developed.
If you are planning for the future, you would want to choose a drive system that is also supported in the future. That is the reason why most electric or hydrogen buses are being equipped with electric mechanisms. This technology will be the basis for the door systems on the vehicle for the next 15-20 years. Future technology that is developed based on an electric mechanism may not work on pneumatic mechanisms.
Due to new regulations and increasing demands for functional safety in door systems, electric mechanisms are becoming more popular. A pneumatic mechanism is generally ‘open loop’ controlled, meaning that the motion of the door is constant from the closed to the open position. With an electric mechanism, the movement of the door is ‘close loop’ controlled by the mandatory door control unit through speed and position monitoring. This means that the movement can be adjusted in unpredictable situations.
Bus door systems: electric or pneumatic mechanism?
The pneumatic mechanism has proven itself in the era of conventional buses. With the change to zero-emissions buses, the electric mechanisms are becoming the standard due to less noise, less dependability on compressed air and less complexity in moving parts, in combination with better control, monitoring and analyzing.
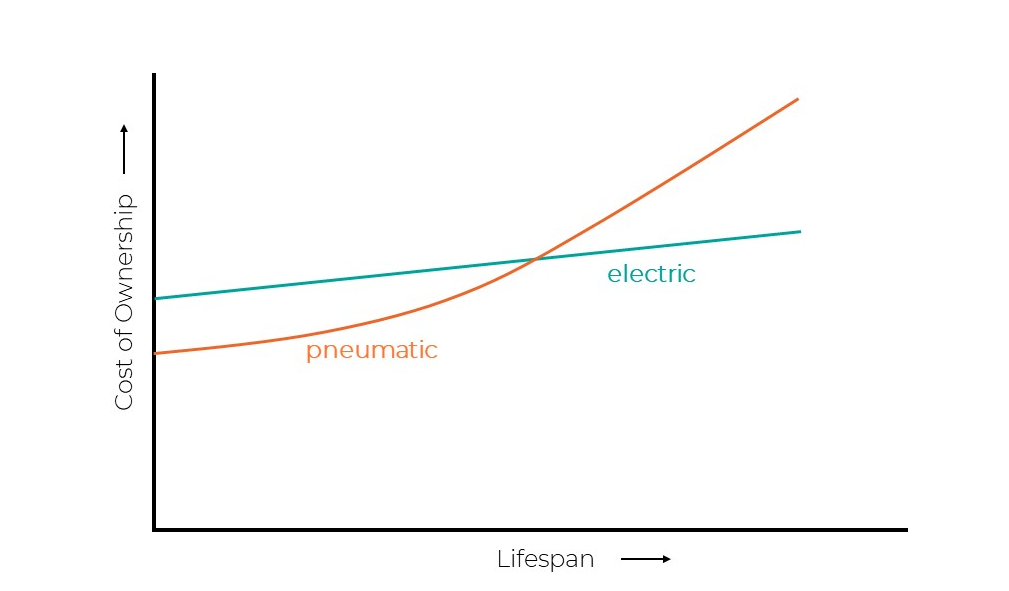
The electric mechanism is a step forward for technology today, but also for future technology. The adoption of electric mechanisms, as for zero emission vehicles, needs to be well considered. There is an investment to be made in implementing this technology within the company, making sure that the electric technology is as well supported as a pneumatic technology would be.
Ventura Systems’ door systems are designed to operate with a pneumatic or electric mechanism which can easily be changed without the need of structural modifications. All changes are made within the mechanism, so parts such as the door leaves or the mounting kit can remain the same. This makes the step from pneumatic to electric very easy, even when retrofitting.