Daimler Truck Battery Technology Center opened in Mannheim. Series production is planned for the 2nd half of the decade
Daimler Truck officially opened the Battery Technology Center (BTC) at the Mercedes-Benz plant in Mannheim, the group competence center for battery technology and high-voltage systems, on July 19. Also cells are to be built there, although “on a pilot basis”. Series production is planned for the second half of the decade as part of the introduction […]
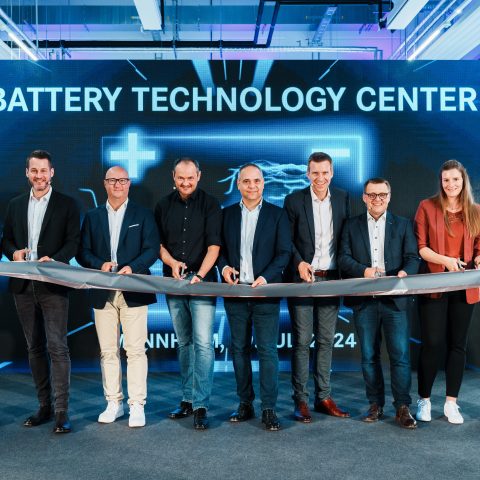
Daimler Truck officially opened the Battery Technology Center (BTC) at the Mercedes-Benz plant in Mannheim, the group competence center for battery technology and high-voltage systems, on July 19. Also cells are to be built there, although “on a pilot basis”. Series production is planned for the second half of the decade as part of the introduction of the next generation of lithium-ion batteries at the plant.
In Mannheim Daimler Buses is currently manufacturing the electric bus Mercedes eCitaro range. The plant is the center of competence for electric city buses and, from 2024, is focusing entirely on the production of fully electric city buses (which in the meanwhile are also produced in France thanks to a recent investment).
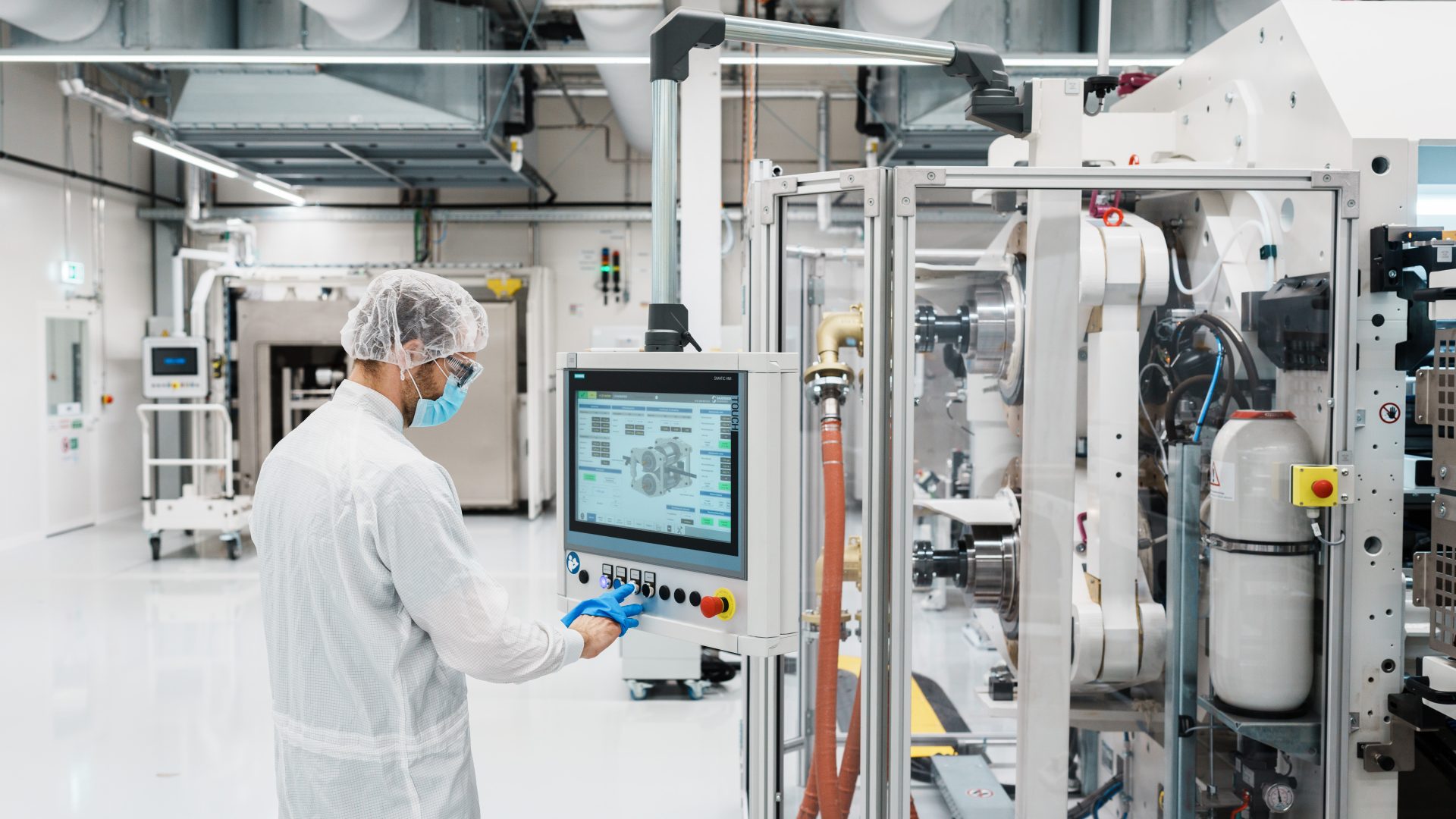
Daimler Truck Battery Technology Center in Mannheim
Daimler Truck’s product and process development for battery electric commercial vehicles is carried out on an area of over 10,000 square meters: the BTC combines development with production. Experts build up knowledge about batteries and their production processes here. To this end, two production areas will be created in the BTC, which was still called InnoLab Battery at the topping-out ceremony.
On the one hand, Daimler Truck states, cells will be produced here on a pilot basis in order to build up process knowledge. Secondly, battery packs will be manufactured as prototypes for test benches and test vehicles. With the pilot line for battery packs, the Mannheim site is preparing for future series production, which is planned for the second half of the decade as part of the introduction of the next generation of lithium-ion batteries at the plant.
Daimler Truck Battery Technology Center goes live
The existing building with the number 18, which dates back to 1952, is located at the heart of the plant and covers an area of 7,500 square meters. In recent months, it has been extensively renovated and extended by a 3,000 square meter annex.
Over 60 new machines and systems are being installed in the BTC, where the relevant processes for the prototypical production of battery cells and systems can be mapped: coating technologies, welding processes, assembly and adhesive processes.
The BTC is divided into two areas. In the cell area, product and process knowledge regarding the manufacturing of battery cells is gained. The equipment provides the prerequisites for gaining extensive knowledge of cell chemistry. For example, it offers the opportunity to experiment with different recipes in the production of battery paste, also known as “slurry”.
This slurry is then used to produce prototype battery cells. Each cell passes through both clean and dry room areas, as it is very important to protect the sensitive materials from dust particles and humidity during production. Both pouch and prismatic cells, two different types of battery cell, can be produced in the cell area. The cell area is used to build up expertise in the manufacturing process and unit scaling.
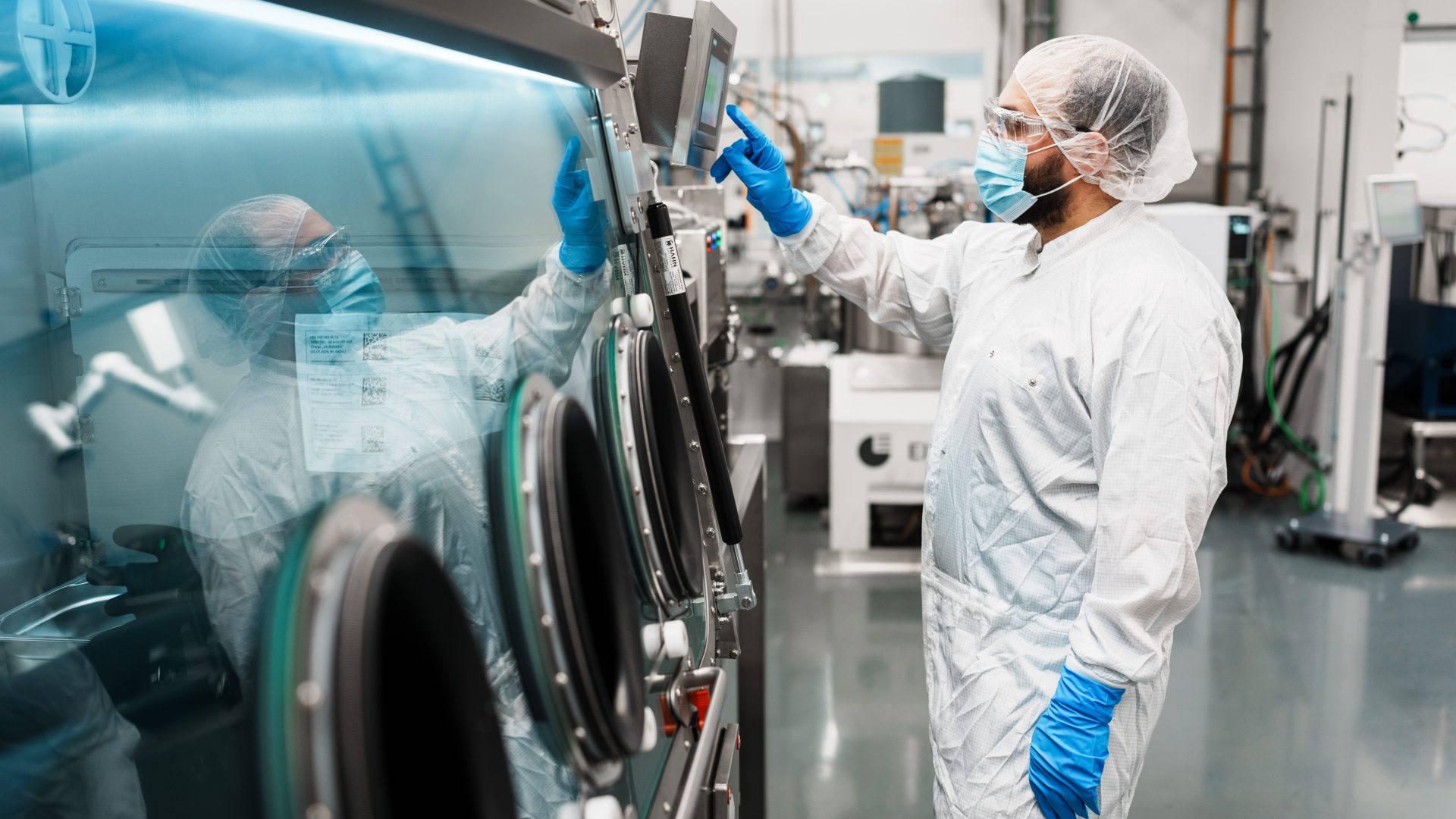
Experience in battery pack assembly is gained on the pilot line for battery pack production: battery modules, the next larger unit within a battery, are manufactured from cells before battery packs are subsequently produced from these modules. In a few years’ time, the findings from this line should go into series production at the Mannheim site.
A total of around 100 employees work at the BTC. In order to give employees more space for creativity, productivity and efficiency, a modern office concept with different work zones was chosen.
Daimler Truck will take care of assembly of batteries internally
Andreas Gorbach, Member of the Board of Management of Daimler Truck and responsible for Truck Technology, states: “The opening of our Battery Technology Center is an important step in terms of electrifying our product portfolio – and yet another milestone in the history of innovation at the Mannheim plant. We have decided to take care of the assembly of the future battery generation ourselves and thus keep important added value in-house. In and for Europe, we will do this at the Mercedes-Benz plant in Mannheim and thereby further strengthen the future of the location.”
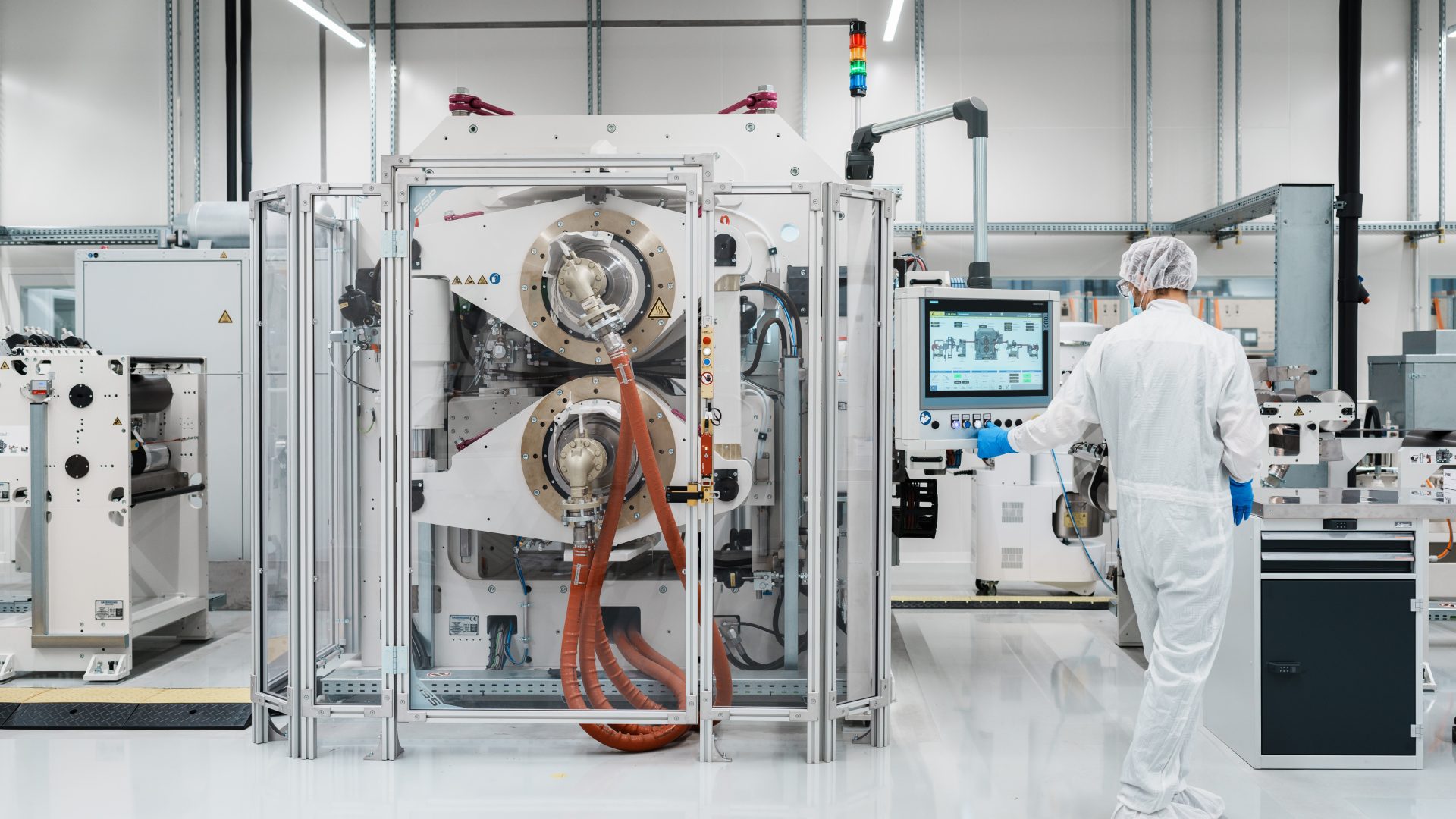
Director-General at the Ministry of Economic Affairs, Labour and Tourism of Baden-Württemberg Michael Kleiner adds: “Battery technology is advancing rapidly and is now a crucial component in applications with the highest performance requirements. Baden-Württemberg must seize the opportunity to become a global leader in battery technology. Our state boasts innovative companies, world-class research facilities, and a highly skilled workforce, giving us a strong foundation to succeed. The opening of the Battery Technology Centre is a crucial step in making Baden-Württemberg a future-proof location and turning the current transformation into a success story.”
Yariş Pürsün, Head of Global Powersystems Operation Daimler Truck, says: “Our aim is to implement new technologies with high added value in our Powersystems plants. With the Battery Technology Center, the Mannheim site is laying an important foundation for the future competence of our own battery technology within Daimler Truck and is driving forward the transformation of our company. In parallel, a second Technology Center at our Gaggenau and Kassel sites is working on future electric drives and high-voltage components.”
Andreas Moch, Site Manager Mercedes-Benz Plant Mannheim: “At the Battery Technology Center, our specialists are working on building up expertise in the production of battery cells and developing assembly concepts and systems for battery packs. We then want to serially produce these battery packs at the site in the second half of the decade. As part of the transformation, the Mannheim site is therefore very well positioned. I would like to thank everyone involved, who have been working hard together on this project for many months.”