Deutsche Bahn’s ICE 3 train fleet travels with renovated Hübner gangways
500 gangways in six years. The Hübner Group has successfully completed gangway renovations for Deutsche Bahn’s ICE 3 trains of the 403 and 406 series. For DB, Hübner met high expectations for the refurbishment of train gangway systems. «The aim of our refurbishment strategy is to facilitate the most efficient possible maintenance for our customers. […]
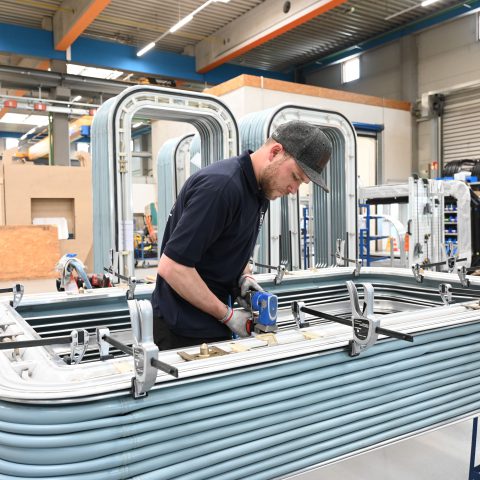
500 gangways in six years. The Hübner Group has successfully completed gangway renovations for Deutsche Bahn’s ICE 3 trains of the 403 and 406 series. For DB, Hübner met high expectations for the refurbishment of train gangway systems.
«The aim of our refurbishment strategy is to facilitate the most efficient possible maintenance for our customers. We made customized arrangements for the ICE 3 together with Deutsche Bahn’s long-distance services at the beginning of the project – with a needs-based technical solution and short throughput times», explains Christoph Steinbach, Head of Sales for After Sales & Service. What is special about Hübner’s concept according to Steinbach is that «Instead of having 1-to-1 exchange of the entire gangway systems, we work out the ideal scheduling and an assembly-based technical solution for each gangway refurbishment. With this approach we aim to reduce the costs and to increase the availability. A solution that is precisely tailored to the overall life cycle of the vehicle and reuses as many components as possible makes our refurbishment both cost-efficient and sustainable».
“The refurbishment of the ICE 3 trains has been a special order for the Hübner company, as we were the original equipment supplier for the gangway systems starting back in 1997. With the completed refurbishment of the gangways, we’ve now made our contribution to ensuring the further use of the ICE 3 trains of the Deutsche Bahn on the rails in Germany and Europe. Our knowledge of the gangway product and of corrugated bellows together with our understanding of the train as a complete system makes us unique in the industry. This product knowledge makes it possible for us to evaluate the technical components very precisely, which in turn allows us to implement highly efficient and customized refurbishment solutions», says Dennis Böhm, Regional Sales Manager, After Sales & Service at Hübner.
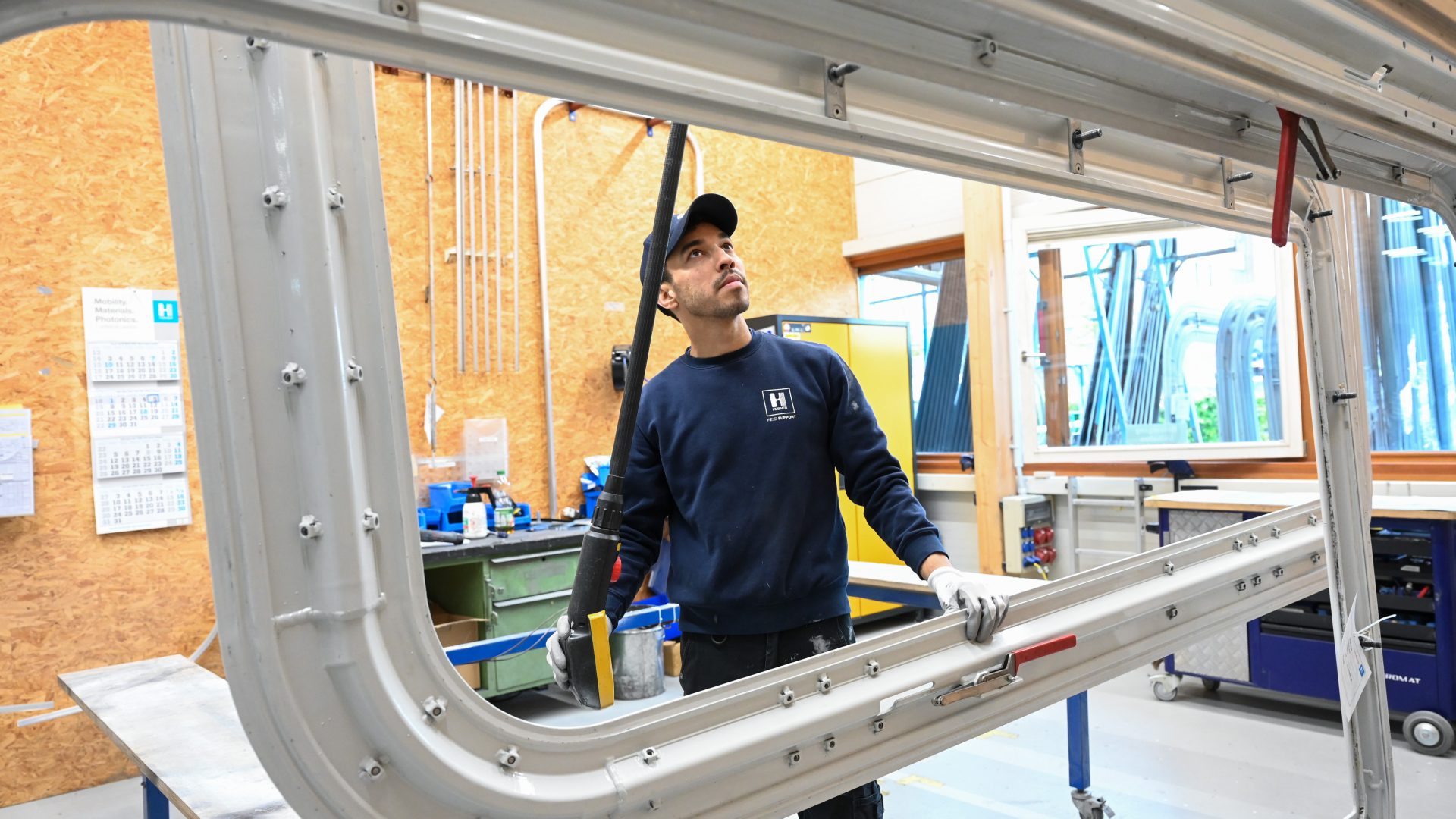
Gangways, reliable quality even at 300 km per hour
Gangways are among the most stressed systems in a rail vehicle, especially in high-speed trains. Gangways and corrugated gussets must act as flexible connecting elements that can reliably compensate for the many movements and forces exerted between individual cars, even at speeds of 300 km per hour. For this reason, gangway systems must be renewed or replaced after 15 years, depending on the routes traveled, climatic factors, hours of operation, and quality of maintenance.
Hübner views after-sales service as a form of product lifecycle management and accompanies its customers as a reliable partner from the beginning throughout the product lifecycle. In addition, Hübner works out individual lifecycle strategies with operators to maximize vehicle availability, as Christoph Steinbach emphasizes: «Our range of services does not end simply with the initial delivery of the main product. Instead, we provide the complete project management, support customers in their individual maintenance strategy and also understand the provision of services in connection with our main product gangway systems as part of our product – and this is customized to the individual fleet requirements and specific conditions in the depots».