Impact Clean Power Technology creates GigafactoryX (in Poland) that will produce a heavy vehicle battery every 11 minutes
A battery for heavy vehicles, trucks and buses, every eleven minutes. Polish company Impact Clean Power Technology (Grenevia Group), has unveiled the render of what will be its GigafactoryX, a large-scale battery factory for electric vehicles and energy storage, to be started in the city of Pruszków, near Warsaw. The production area of GigafactoryX will […]
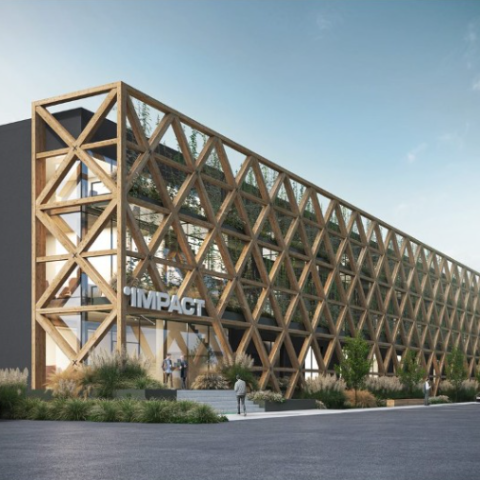
A battery for heavy vehicles, trucks and buses, every eleven minutes. Polish company Impact Clean Power Technology (Grenevia Group), has unveiled the render of what will be its GigafactoryX, a large-scale battery factory for electric vehicles and energy storage, to be started in the city of Pruszków, near Warsaw.
The production area of GigafactoryX will be 16,300 m². The factory will include, among other things, a battery testing facility and a research and development center. Batteries will be produced for various types of electric vehicles, including those for public transportation, such as e-buses, e-trucks, and the rail sector. The plant will also produce energy storage systems designed for the commercial electric industry, including for large-scale electricity storage. The battery systems will be based on lithium-ion cells in the technologies: LTO, LFP and NMC.
The modern plant will be one of the largest of its kind in Europe. Its construction will increase Impact’s production capacity to 1.2 GWh in 2024 and to more than 4 GWh per year in 2027. An energy storage facility for about 1 MWh is also planned, which will work together with the PV plant and the power grid.
Potrebbe interessarti
Impact Clean Power Technology to open a battery systems’ factory in Poland (will bring production capacity up to 5 GWh/year)
Impact Clean Power Technology explains the GigafactoryX project
“The GigafactoryX project is another big step in the development of Impact Clean Power technology. The first phase of the investment will allow us to increase production capacity to 1.2 GWh per year as early as next year, through which we will ensure the security of supply of battery systems for major global brands, which are our partners. Finally, in 2027, production will reach 4 GWh per year. The creation of GigafactoryX means that Poland will be the leading European supplier of batteries for the electric mobility industry, all based on Polish solutions,” comments Bartek Kras, CEO of Impact. “In addition, it is extremely important for us that the new plant is designed according to the principles of sustainable development,” he adds.
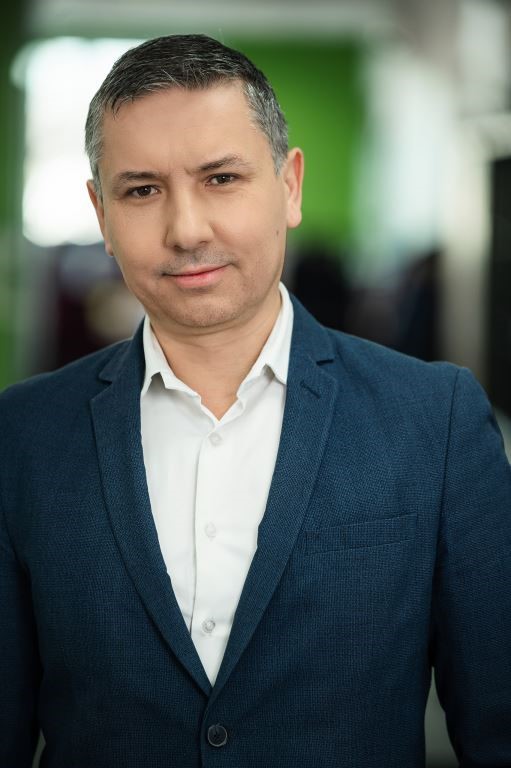
The company teamtechnik Production Technology Poland is responsible for the supply and installation of the public transport battery production line at the GigafactoryX.
The first-phase line has dimensions of 58 by 19 meters and is thus the largest project realization in the history of teamtechnik Poland for battery systems. Fourteen engineers worked continuously for four months on its mechanical, electrical, and automation design. The line’s flexibility is influenced by the use of a production cycle, which allows production to be optimized according to the type of product. As a result, it provides space and cost savings for the investor. The safety of employees working on the line is ensured by thermal cameras; when a high module temperature is detected, the product evacuation procedure is triggered.
The teamtechnik solution is also a key element in increasing Impact’s production efficiency. By 2024, the line will enable the production of 16,000 units of battery systems, up from the current capacity of about 2,500 units. It will also ensure reproducible product quality, as it includes full automation of processes such as robotic assembly of individual components, batching, screwing, visual inspection, and a series of tests. For the first time in the world, Bosch Rexroth’s TS7 conveyor system will be used. Assembly work is scheduled to begin in July 2023.
“Thanks to the high automation of processes, we are increasing not only the efficiency of production, but also the quality of the batteries produced. The effect of the technologies used will be a rapid assembly cycle of a single battery, which will be only 11 minutes. This is of great importance in view of the growing popularity of electric mobility and the predicted increase in demand for battery systems in Europe,” comments Bartek Kras. “Our collaboration with teamtechnik is an example of cooperation and synergy between companies that are part of TDJ. The combination of our expertise and development potential within one group allows us to gain significant market advantages. The support of TDJ and Grenevia is an important support for business development and scalability,” he concludes.