Inside BorgWarner Gigafactory in Darmstadt, equipping 20% of e-buses in Europe and US
BorgWarner welcomed us to its Gigafactory in Darmstadt. The plant can produce about 35,000 NMC battery packs in a year using innovative, highly automated lines. Investments in LFP batteries are planned to expand the company’s portfolio with products addressed to several sectors, from buses, to trucks, up to special vehicles. Here's what we saw in Germany.
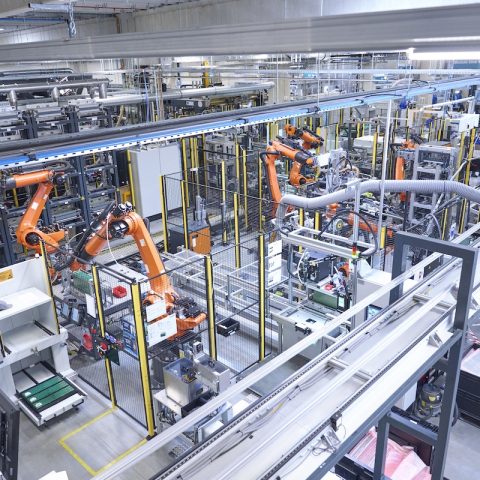
Where there was nothing before Covid, there is now one of the best-equipped gigafactories in Europe. The largest one excluding those belonging to OEMs. The acquisition, which was finalized in 2022, gave BorgWarner access to the battery production plants of former Akasol that now works on three shifts, five days a week using state-of-the-art, highly automated production lines.
Our sister media Sustainable Truck&Van has been visiting BorgWarner headquarter. This is an extract of their reporting from Darmstadt. You can read the integral article HERE
Trucks, buses, off-road vehicles (excavators, snow groomers, aerial platforms) and marine applications are the ones of choice for BorgWarner batteries, with the addition of projects in the field of eTrailers. So far, the bus sector has been very relevant: according to the American group, one in 5 e-buses in Europe and the U.S. mounts BorgWarner batteries.
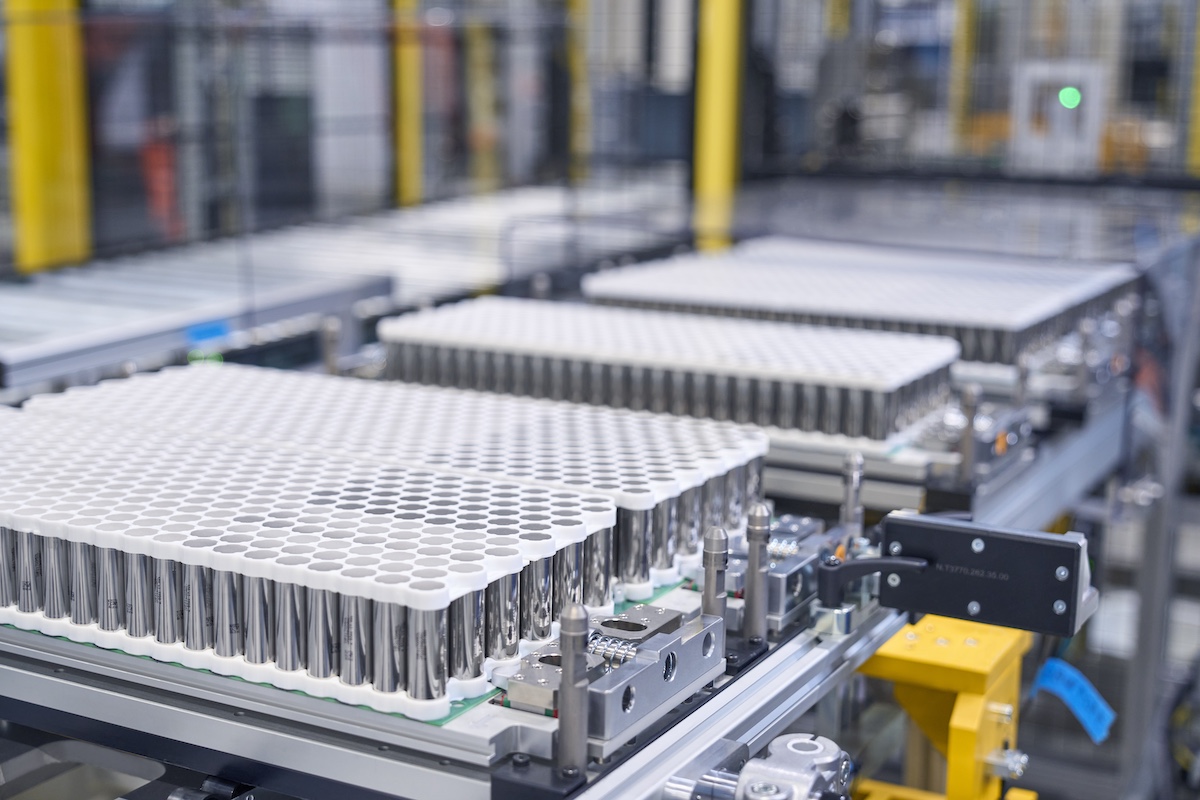
BorgWarner Gigafactory in Darmstadt: what we have seen
In Darmstadt, not far from Frankfurt, production, testing area, offices and R&D occupy about 15,000 square meters, plus 4,000 square meters at the nearby Langen site. A total of more than 850 people are engaged in the design and manufacture of battery modules and packs, as well as BMS (Battery management systems) and Removable Contactor Box.
In a nutshell, as of 2022 in Germany alone, BorgWarner’s battery systems division has produced about 5 GWh of battery packs for commercial and industrial vehicles using NMC (Nickel-manganese-cobalt) technology. This is set to increase significantly when the site’s maximum capacity of 3.5 GWh is reached, thanks in part to the finalization of a second highly automated production line. Considering also the other U.S. plant in South Carolina, the group expects a production capacity of about 5.4 GWh in 2025.
BorgWarner engineers showed us how the assembly lines work. It begins with the insertion of cylindrical cells inside the modules: the third-generation battery packs currently produced by BorgWarner admit two layers of 300 cells, for a total of 600 cells per module.
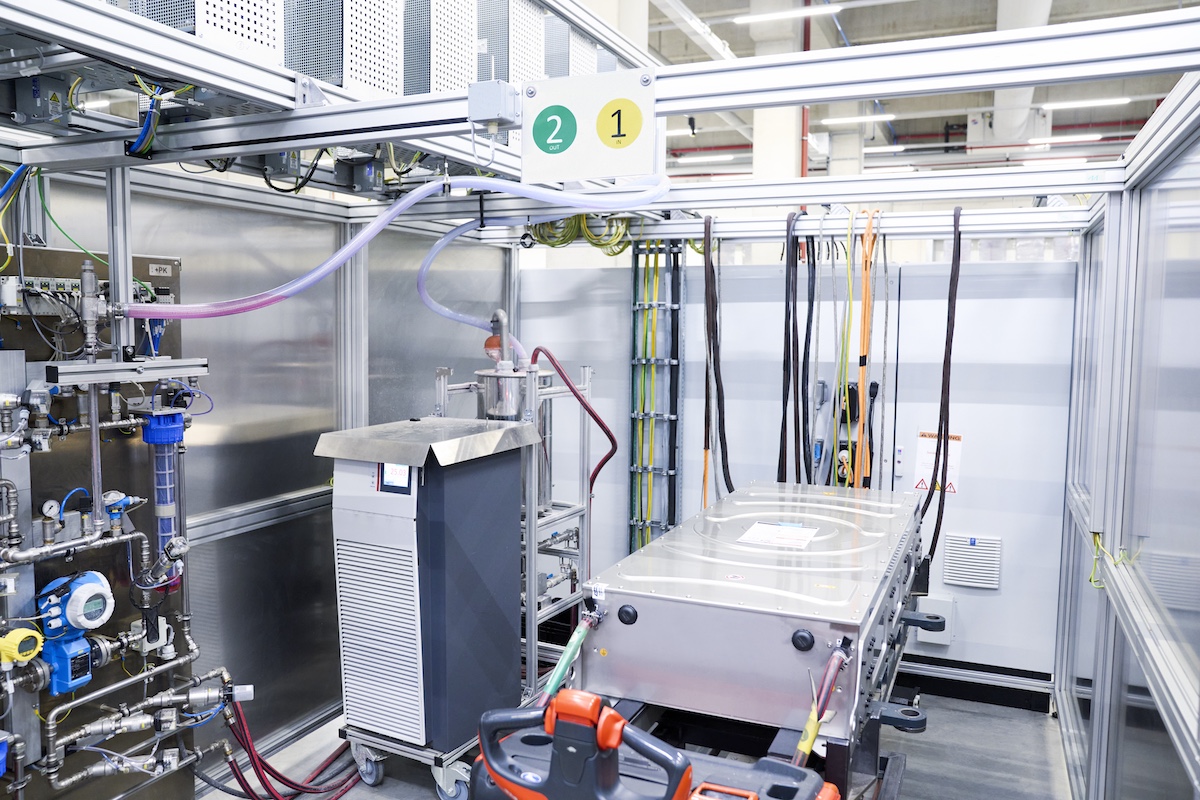
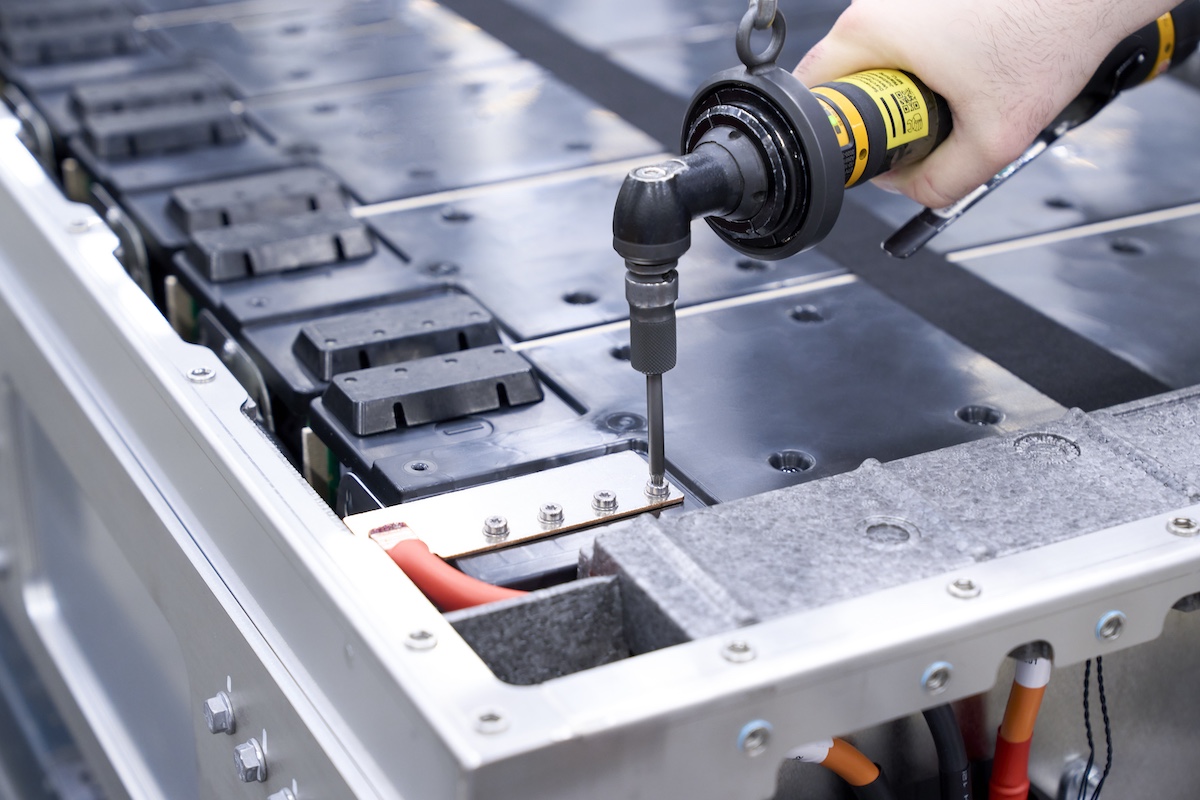
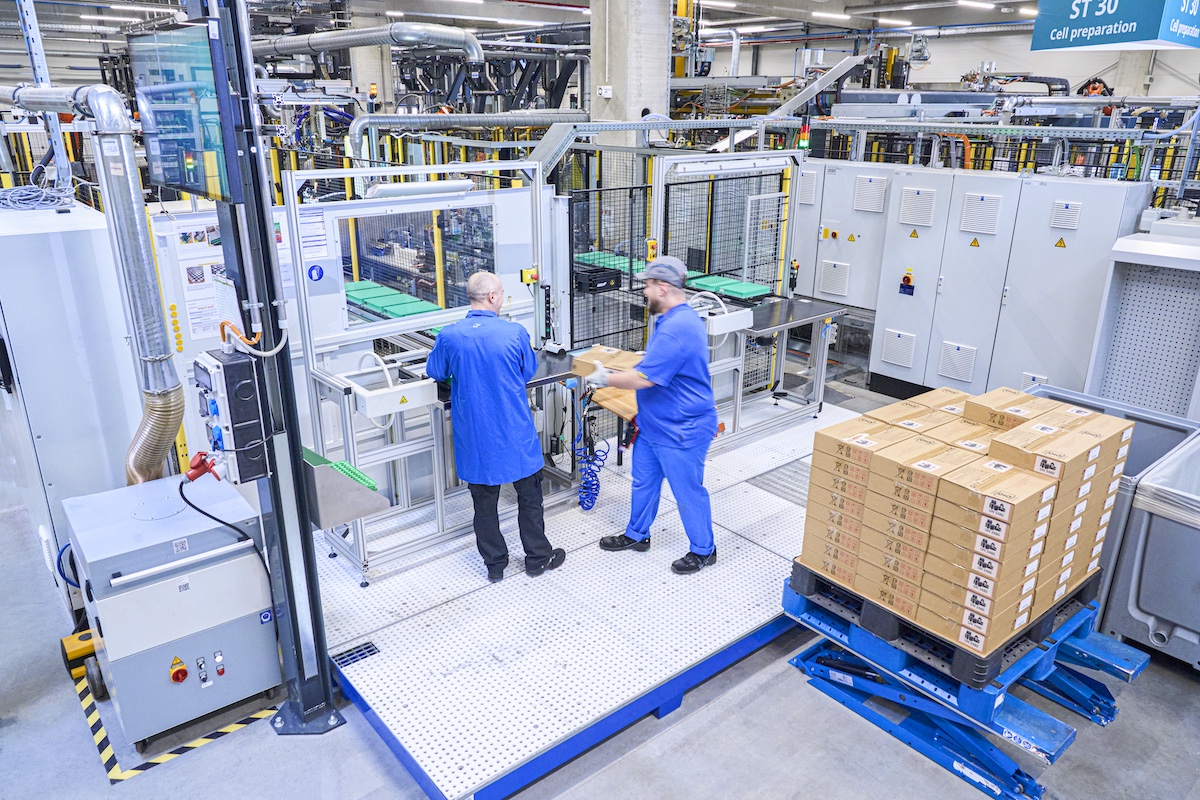
The processes of gluing (including preparing the cell surface) and adding the electronic connections – which are both entrusted to robots – is the most complex part. It takes more than one hours to manufacture a single module, which weighs about 50 kilograms, with an interval of a few minutes between the production of one module and the next.
The production process of the battery packs, then the insertion of modules, is relatively simpler and is also entrusted to industrial robots for reliability and weight management issues. There are very few manual tasks overall, mainly feeding and operating the machines. Every around 20 minutes, the line makes a 9-module battery pack.