Mechanical stress and physical damage as causes for battery fire
The terrible incident that occurred in Mestre/Venice on the evening of Tuesday, October 3rd, has relaunched the debate on the challenges posed by electric vehicles in terms of fire risk. The electric bus, manufactured by the Chinese group Yutong (the largest bus manufacturer in the world as well as one of the top sellers world […]
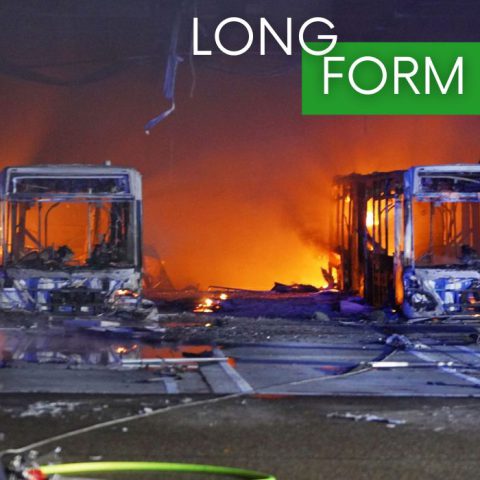
The terrible incident that occurred in Mestre/Venice on the evening of Tuesday, October 3rd, has relaunched the debate on the challenges posed by electric vehicles in terms of fire risk. The electric bus, manufactured by the Chinese group Yutong (the largest bus manufacturer in the world as well as one of the top sellers world wide of battery-electric buses), has been registered in early 2023 (therefore brand new). It crashed through a barrier and fell nearly 15 meters (picture below, while the opening one refers to a fire occurred at Stuttgarter Straßenbahnen’s depot in October 2021). 21 passengers were found dead.
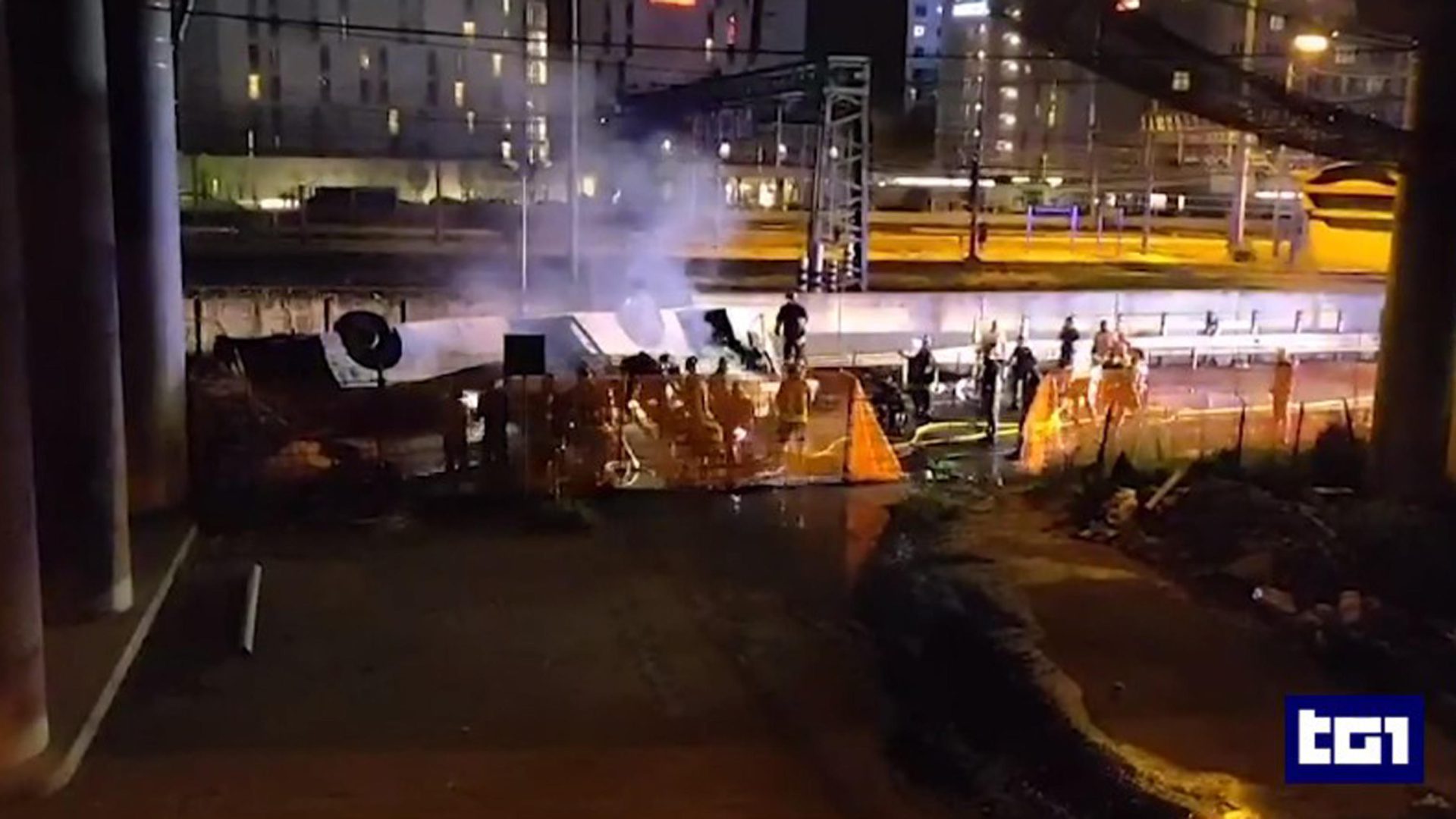
As reported on the BBC, “Fire brigade commander Mauro Longo told Il Gazzettino website that the bus’s batteries caught fire and made the task of clearing the bus a complex operation”.
Let’s now focus, thanks to a new contribution by Claudius Jehle, CEO of volytica diagnostics GmbH (already author of the knowledge articles series The Battery Cycle), on the relations between batteries and fire risks.
Despite the fact that electric vehicles are – according to various statistics – much less likely to burn than internal combustion engine vehicles, they still do in times. And once on fire, most Li-ion battery subtypes including NMC and LFP irrespectively of the cause, are extremly difficult to extinguish.
The reasons for catching fire are manifold; particularly dangerous and insidious are cell-internal, electrochemically-induced defects that grow over time due to heavy or abormal usage, such as frequent fast charging or operation in cold environments of (particularly) NMC-based Li-ion batteries. Once grown to large, they perforate cells internally, connecting the positive and negative electrodes internally and thus causing a localized, seamingly miniscule short circuit that can lead to cell breakdown or – in the worst case – more short circuits and thus an avalanche of hot-spots – the infamous thermal runaway.
Such internal defects – a particularly prominent one being ‘Lithium plating‘, the formation of metalic formations inside of cells – are a challenge on their own, as their macroscopic influence is subtle, and trends make themselves noticably only on timescales greater than local electronic systems can reliably process. This is much like cancerous tissue in living organisms – over very long periods virtually undetectable, but once such tissue makes itself noticable macroscopically, it is often too late to take appropriate action. In both cases, only carefully longterm monitoring with the right detection systems can mitigate the particularly challenging risks of cell-induced fires.
It must be stated in all clarity that each and every Li-ion subtype has their own sensibility and susceptibility to usage conditions, and while for one type, fast-charging at low temperatures (e.g. for the latest Ni-rich NMC-types) is critical, it might be totally acceptable for another (e.g. LTO). You have read correctly – the latest, i.e. the newest, NMC technology is particularly delicate when it comes to robustness. The ‘hunger’ for range and energy density comes at a price: adding more Nickel increases range, but reduces self-ignition temperatures, cycle stability and the inclination towards Li-plating. LFP is believed to be more robust in that aspects, but once on fire, for whatever reasons, LFP burns as violently as other types – some researches even state that LFP is particularly prone to vapour cloud deflagrations.
But what about external events, incidents and mechanical stress?
The current consensus is that many, if not most, fires are caused by auxiliar components or other battery-unrelated sources. Overheating charging plugs, faulty insulators and cables (there are many, many cables inside a electric vehicle) or external heat sources will cause any Li-ion battery to burn with the rest, whilst not causing the fire. Those fire sources are likely to diminish with manufacturing maturity over time, while this is not equally true for the above-mentioned, electrochemically-induced sources.
The case of mechanical stress counts as an in-between. A very typical experiment to assess the safety of new cells is the ‘nail penetration test‘ – a nail is driven through a cell, and the effects are recorded and measured. Typically (but again, varying with cell-chemistry) one sees flames and/or vapour erupting from the spot, soon to ignite or otherwise explote – try searching the internet for video footage. If you recall the process of internally-triggered fire from above, this must not surprise you: a conductive metal short-cuts the positive and negative electrodes, in this case not subtle and growing internally over weeks and months, but immediatly. However in essence, the same mechanism: connecting what’s to be separated, unleashing of a lot of energy in very short time, localised hot-spots, self-enforcing repetition, thermal runaway.
Imaging a shock, an accident, a sudden compression due to a crash or penetration of a battery system by external or vehicle-bound materials (e.g. trusses) – high probablility of a critical damage. Particularly mean are cases without obvious indentations – in absence of visual cues one must rely on external diagnosis tools, because again, the local electronics are made for safe operation, not for the edge cases of total descrution. Imaging such ‘lite shock’ event has caused some damage, again not enough for a full-scale imminent event. Such pre-damage can very likely greatly increase the likelihood of premature failure later on, due to much less than another major impact.
How to best extinguish a burning Li-ion battery?
There are numerous claims on the internet and in commercial advertisements. The least common denominator might be that vast amounts of water help contain the brutal effects of burning batteries best.
To summarize: In some cases, cell-internal, usage-induced defects cause battery fires. It is believed that many more cases are due to external forces, which can very likely trigger an imminent, and even delayed fires. Any damaged battery must be treated with utmost care. Like with monitoring human health – don’t rely on a doctor only when push comes to shove, but treat the most expensive wearing and tearing component of the mobility transition with a minimum of care and attention.