SnapXit emergency exit, the safety device developed for buses and coaches
Using sustainably sourced energy to power the buses of today and into the future is compelling and logical, but in order to bring the conversation of sustainability on a more wholistic level, as much of the vehicle as possible should have as small an ecological footprint as possible from materials to longevity bringing longer service […]
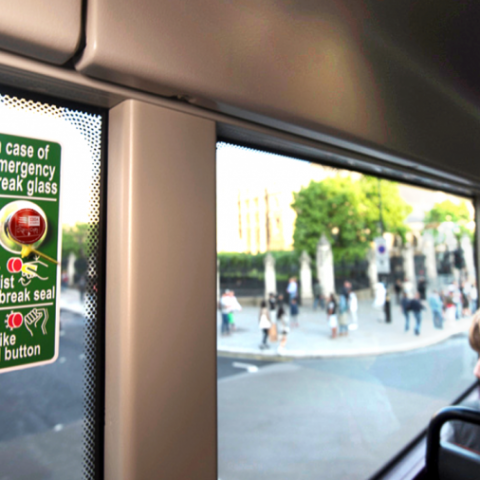
Using sustainably sourced energy to power the buses of today and into the future is compelling and logical, but in order to bring the conversation of sustainability on a more wholistic level, as much of the vehicle as possible should have as small an ecological footprint as possible from materials to longevity bringing longer service intervals and lower running costs.
It’s the goal of SnapXit emergency exit devices for bus (among other applications), which are gaining ground as an alternative to the classic glass-breaker hammer.
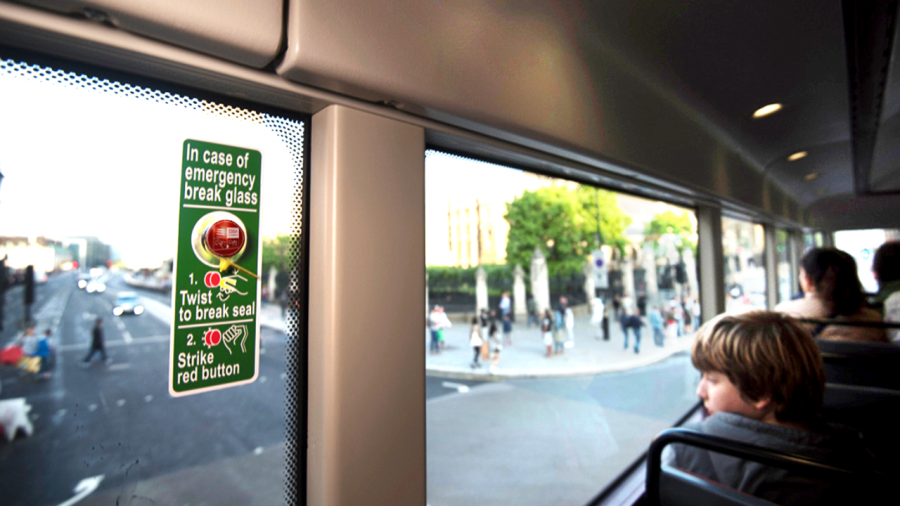
Emergency exit devices with the bus in mind
SnapXit system, which is part of SafeTSystems’ portfolio, is an emergency break glass device capable of breaking safety glass in an emergency. SnapXit has been developed with the assistance of bus manufacturers and today has customers in 17 countries in the world. SnapXit technology consists of a hard material impact tip able to penetrate toughened, tempered, or safety glass.
SnapXit emergency exit devices for bus «are popular for many reasons, most of which are pretty evident in high quality, genuine performance and maximum accessibility – the producer says -. Operators and OEMs the world over have adopted simple scientific capability over old school dogma. Analysing competitor hammer systems scientifically is a no-show compared with our purpose built emergency exit systems. There are a few less obvious SnapXit advantages that go directly to the heart of the sustainability that all manufacturers and operators are pursuing. We have identified advantages in production cost, environmental impact, and operational and running costs».
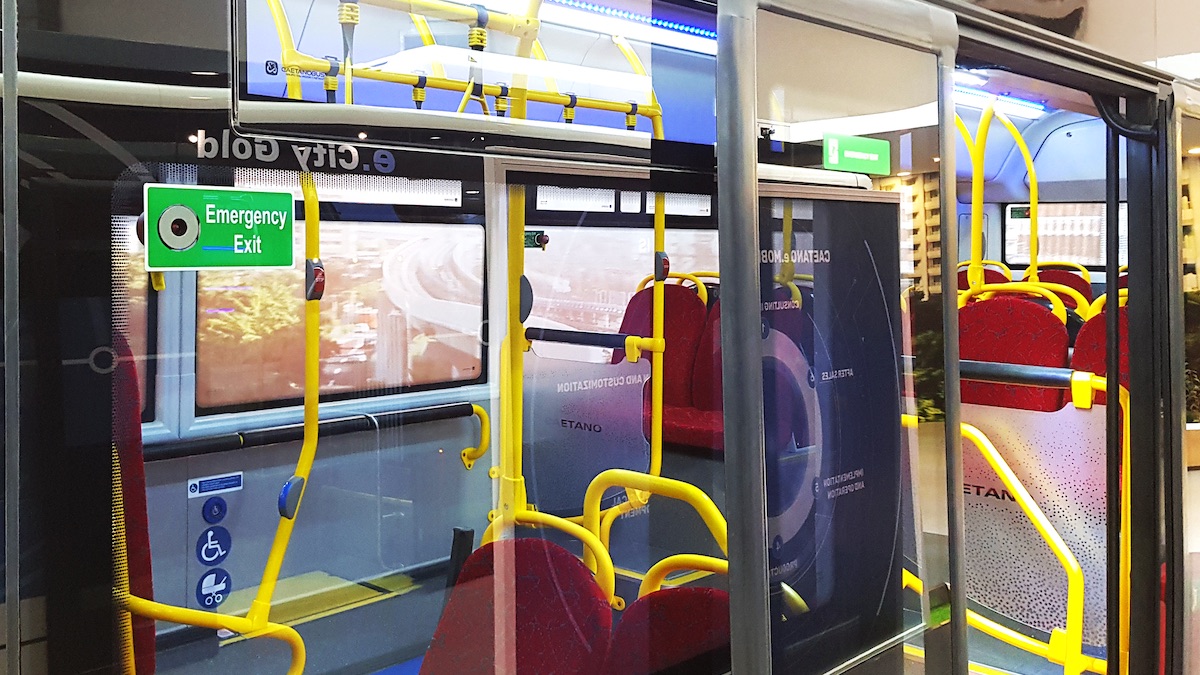
Five-step fitment procedure for SnapXit system
SnapXit’s emergency exit device for bus vehicles requires a quick five-step fitment procedure, as an operator retrofit or as original equipment. It means a vehicle manufacturer can successfully shorten the production line by a station. For some OEMs, this represents a full day’s saving. Skills, materials, and fastenings to fit a hammer are replaced with isopropyl alcohol, a squeegee, and some paper towelling.
From the environmental point of view «we also step forward – still the company speaking -. SnapXit emergency exit devices are made with stable, non-degradable, and rustproof materials, and therefore effective as emergency exit devices for the lifetime of the vehicle if properly installed, then eliminating the need for the hammer’s plastic cabinets, brackets, handles, and wiring which can all perish, crack or degrade over time needing to be repaired or replaced».
Finally, running and operational costs. Maintaining hammer systems brings vandalism, theft, and off-bus crime that can lead to a vehicle being taken out of service to repair and re-certify, while a SnapXit system suffers none of these problems. In all, with sustainability as a driver to change in sourcing, design, and efficiency, we need to see modern buses as more than just clean, clever drive rolling chassis if the term is to remain relevant into the future.
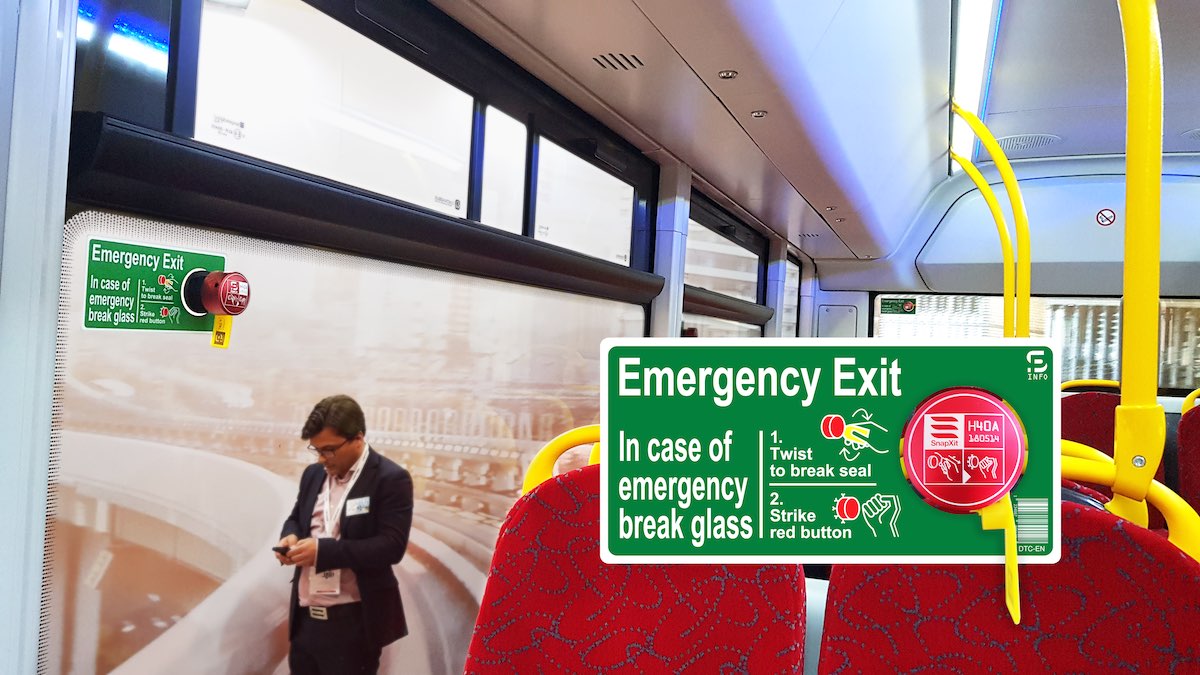