Voltabox presents a battery technology suited for a cell-to-vehicle approach
Voltabox has presented a new technical concept (named Flow-Shape-Design) for the production and design of lithium-ion batteries. Main feature: a flexible design which allow the battery to fit assembly spaces and be potentially integrated in segments of the body. The new technology will be available to battery manufacturers and OEMs from the summer of 2021 via licensing […]
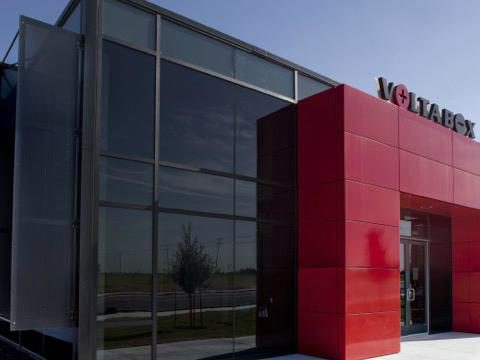
Voltabox has presented a new technical concept (named Flow-Shape-Design) for the production and design of lithium-ion batteries. Main feature: a flexible design which allow the battery to fit assembly spaces and be potentially integrated in segments of the body. The new technology will be available to battery manufacturers and OEMs from the summer of 2021 via licensing model.
With its innovative Voltabox Flow-Shape-Design technology, Voltabox expects this to provide a developmental leap forward for the entire battery industry. With the goal of widespread use, in the future the Group will also make its protected technology available to selected markets via a licensing model. The method enables the use of all available cell types.
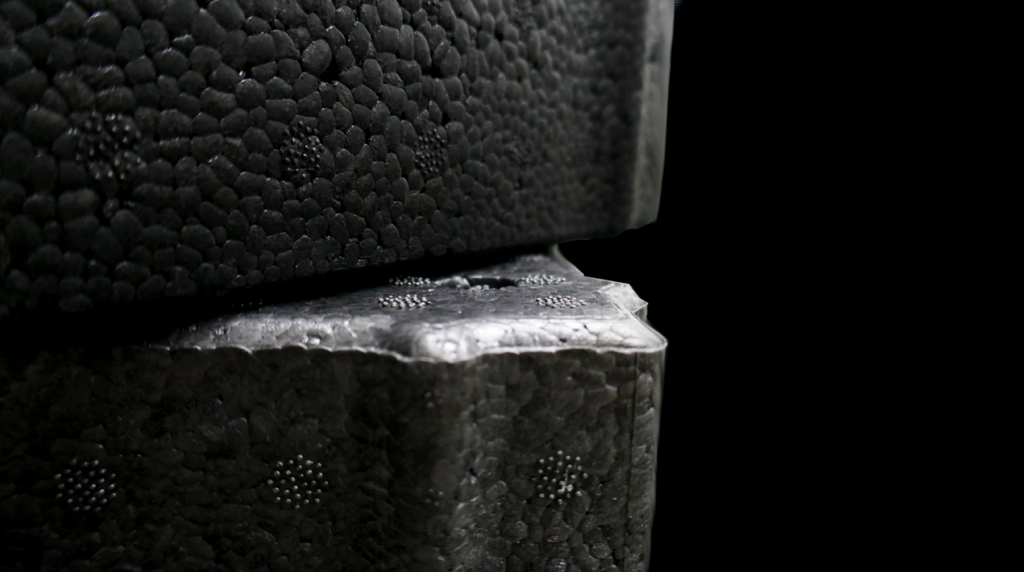
Voltabox battery with self-strengthening materials
By means of a structured innovation process, Voltabox has developed and protected a new production method which greatly simplifies the design of Li-ion batteries, the German company points out. The key feature of this technical concept is the use of the type of self-strengthening materials which are also used in the aeronautics industry.
The usage of these materials for the casing, Voltabox explains, «makes it possible to produce high-performance batteries very inexpensively and in virtually any conceivable free form. The battery cases of the future will no longer require relatively heavy screwed or welded metal parts. To date, these have been considered essential in order to ensure the robustness of the accumulators. The additional weight which this entails and the rigid casing have generally defined the limits for battery application design».
In the future, self-strengthening and ultimately rigid plastic will enable a significant weight reduction at the modular and system level and thus significantly improve the cost efficiency of Li-ion batteries, according to the supplier.
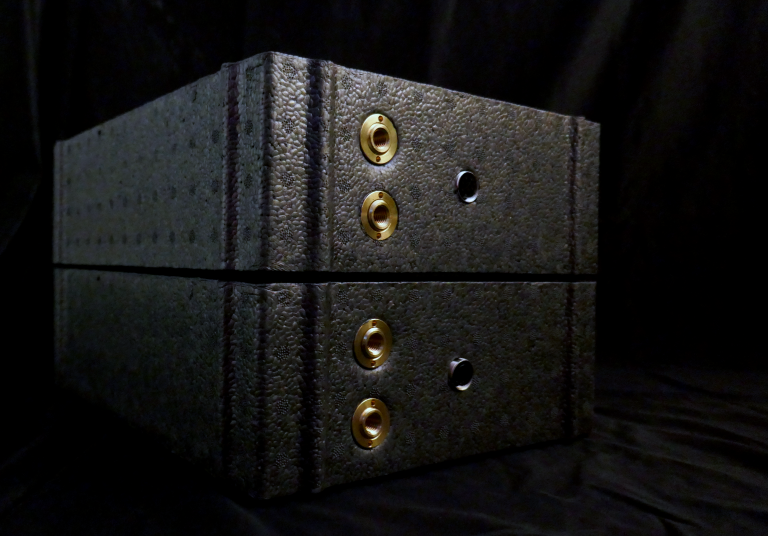
Voltabox batteries and the cell-to-vehicle approach
Voltabox Flow-Shape-Design also delivers high flexibility in the area of battery shape. Assembly spaces can thus be used with much greater precision. Completely new integration options are even possible, such as in defined segments of the body. This entirely novel technological method using self-strengthening materials enables a cell-to-system (already embraced by CATL, for instance) or even, in the broadest sense, a cell-to-vehicle approach.
Voltabox Flow-Shape-Design, licensing models
As of the market launch of Voltabox’s Flow-Shape-Design in the summer of 2021, the Group will therefore add licensing to its business model. Several patents have been filed for this purpose, while utility models and trademark rights have already been protected. Voltabox says it is now successively starting talks with customers on the use of the technology. The method enables the use of all available cell types.
“With its Flow-Shape-Design concept, Voltabox will initiate a revolution in the lithium-ion battery industry. This was only possible because we called into question every one of the current technical assumptions relating to battery design. We were thus able to establish the basis for a manufacturing process for batteries which will make them significantly lighter, more flexible and cheaper. This really is a groundbreaking development,” says Jürgen Pampel, CEO of Voltabox AG.
Voltabox Flow-Shape-Design batteries, attractive pricing
“Our conceptual innovation is extraordinary and disruptive because we have provided an answer to the key limiting factors for the use of lithium-ion battery technology, such as weight, system price and complex production methods. Flow-Shape-Design considerably reduces battery weight at the system level by comparison with conventional products. Moreover, a significant reduction in the number of individual parts, the use of low-cost materials and the relatively simple production process enable pricing which is significantly more attractive than the current market level,” Patrick Zabel, CFO of Voltabox AG, says.
Jürgen Pampel notes: “Flow-Shape-Design is suitable for any type of battery application. The cost-saving potential will depend on how important factors such as weight and assembly space are for the vehicle type in question. However, in our view the strengths of this technology will make themselves felt not only in the traditional fields of application which Voltabox has catered for to date. For boats, aircraft and stationary applications in particular, the advantages of Flow-Shape-Design are obvious.”